The cement industry is energy-intensive, with a considerable carbon mark threatening environmental sustainability. The annual emissions of the concrete industry are up to 2.8 Gt CO2, and it is estimated that concrete production accounts for 9% of overall greenhouse emissions, and it is predicted that 9% of overall greenhouse emissions originate from concrete production, and cement plants account for 7–8% of carbon dioxide emissions worldwide. The two approaches for addressing the impact of the greenhouse gas from the cement industry are as follows: improving the cement production process efficiency, and partial replacement of normal cement with supplementary cementitious materials (SCMs). There are different SCMs for decreasing carbon dioxide release and improving the durability and mechanical characteristics of concrete, which include as following: ground-granulated blast furnace slag, silica fume, calcined clays, nano clay, natural pozzolans, carbon nanotubes, graphene oxide, nanoTiO2, nanoZnO2, nanoCaCO3, nanoFe2O3, fly ash, nanoSiO2, nanoAl2O3, and rice husk ash. In this project, we analyze the durability and mechanical properties of concrete containing nano additives under different loading regimes, curing conditions, and freeze-thaw processes.

Seyed Morteza Seyedpour
Dr.-Ing.Head of Laboratories, Head of Experimental Mechanics & Enviromental Engineering Group, Researcher
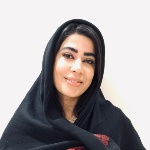
Omolbanin Arsteh-Khoshbin
M. Sc.Research Assistant